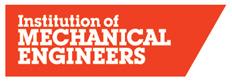
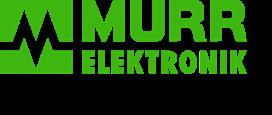
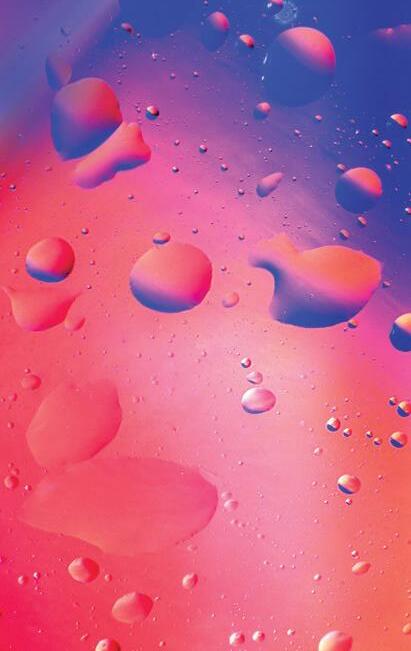
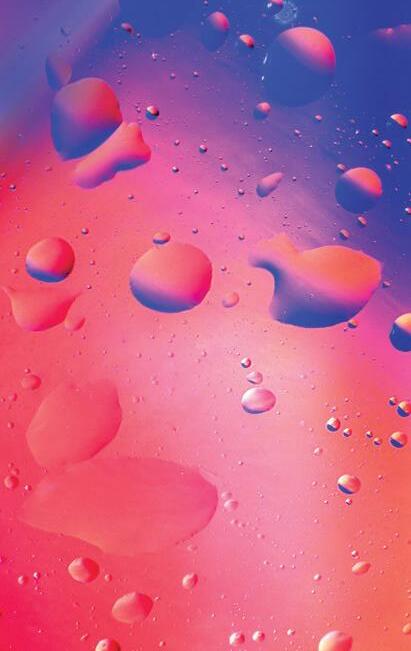
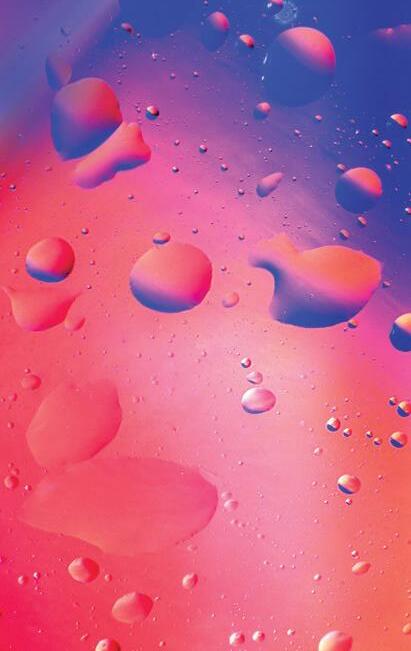
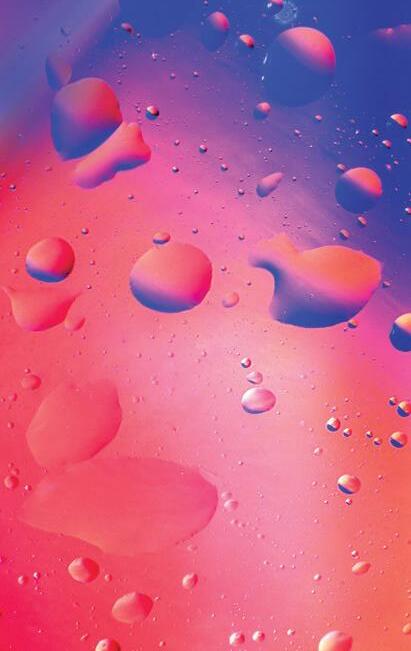
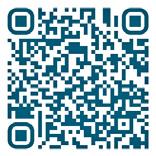
The subject of energy, or rather energy efficiency, has long been a topic of vague disinterest among the vast majority of households and billpayers. Energy, or rather the complex business sector that produces and delivers it, has historically struggled with engagement. Energy efficiency, in particular, has more often than not been misrepresented as simply a penny-saving exercise involving the change of lightbulbs for modern replacements, and switching lights off when rooms are unoccupied. Boiling the kettle less, another suggestion often heard.
However, with the huge global rise in the cost of energy, and its near constant headline coverage by the broadcast media, not to mention the financial pain we are all now enduring, perhaps 2023 has the potential to see a real change in attitudes. A change that could positively impact all aspects of energy use.
Of course, greater autonomy in our energy provision is now understood and acknowledged as a stand out
way to protect ourselves from market volatility caused by unstable regimes. But the drive for improved efficiency across all the avenues of energy use, will simply mean that the energy we do produce and secure as a country will go that much further. This will not only allow us to make big savings on our domestic bills and to ensure our homes stay warm through the winter months, it will also have a massive impact on the efficiency, and ultimately, the profitability of our commercial and industrial sectors.
The British Pump Manufacturers Association (BPMA) has been a longstanding advocate of not only the need for improved energy efficiency across the UK’s vast installed base of pumps and pump systems, but also the massive opportunity it presents for significant energy use reduction.
The operation of pumps and their associated systems accounts for around 20% of the world’s entire electrical energy consumption, and in some high-use industrial applications, this can be as much as 25-50% of the total electrical energy usage. Across
the European continent pumps are the single largest user of electricity within industry, consuming over 300 TWhpa of electricity, which in turn accounts for over 65 Mton of CO2 emissions.
Unfortunately, the vast majority of pump systems operating today were not originally designed with energy conservation as a major consideration. It is now well documented that rotodynamic pumps, which account for 80% of the installed base across Europe are between 20-30% oversized. This is usually due to an in-built ‘safety factor’ allowing for potential future uprates, or any wear in the pump or fouling of the system. But this simply means they are using far too much energy for the required duty. As such, there is huge potential to save massive amounts of energy if these pumps are properly sized, operated and maintained. In fact, if pump systems are initially designed with energy use in mind, and the pumps are optimised for efficiency, a saving up to 50% in electrical energy can be achieved.
Steve Schofield, CEO at the British Pump Manufacturers’ Association, considers whether there is at last a change in attitudes towards energy efficiency amongst the general public. And if so, whether this can have a meaningful impact on decreasing the energy consumption across UK industry.
In essence, it is important to know as much about the pump system as possible and to create a pressure/flow profile for the system, as the energy required to drive the pump is directly related to the flow and pressure required.
It is also important to carry out regularly energy audits to help determine where energy use reduction measures can be employed, and in turn how operating costs can be lowered. The government has estimated that most companies can reduce their energy consumption by 10-20%, and energy audits carried out in accordance with ISO 14414 have shown that savings of 30-50% are not unusual. By reviewing utility bills, you can get an indication of the savings to be made and the investment that you should be prepared to put into the auditing process.
Across most industrial sites, some two-thirds of the total energy consumption is used to power electric motors, an integral part of any pump system. The overall cost associated with operating these essential pieces of equipment throughout their entire life span can be broken down as follows; 5% accounts for the initial purchase/installation costs, 10% for ongoing maintenance and a massive 85% for the energy used to run them.
Clearly, any reduction in the energy consumed by electric motors is important, and with modern designs, that reduction can be as much as 30%. It is also evident that many pumps and motors are constantly
operated at full power, irrespective of process needs, something which can managed with the addition of variable speed drives, and so across Europe’s installed base there is the potential for significant energy savings; savings which can in turn drop to the bottom line and increase the profitability of any business.
Given the amount of energy consumed by pumps in their normal operation, and the potential for energy efficiency gains within pump systems, the BPMA has developed the Certified Pump System Auditor Scheme (CPSA).
Through the CPSA, pump engineers are being trained to correctly assess the efficiency of pump systems, and to provide appropriate recommendations in order to improve the efficiency of those systems. The CPSA accreditation is achieved by successfully completing a four-day residential course, followed by the satisfactory completion of a pump system audit. Only then can ‘Certified Pump System Auditor’ status be achieved.
Within the full ESOS Guidance document, the ISO/14414-Pump System Energy Assessment standard is referenced as an auditing methodology that can be accepted by “Lead Assessors” approved by the Environment Agency. Accordingly, it is hoped that CPSA accredited persons (who are trained according to the IS0 14414 standard) will be recommended
by Lead Assessors to undertake the pumping system elements of company-wide energy audits.
The next CPSA Training Course is scheduled for 9th-12th May 2023. For more detailed information, please visit http://www.bpma-cpsa.co.uk
In conclusion, it is hoped that with the heightened publicity around the cost of energy, and society’s growing appreciation of its importance to our very existence, we will begin to see far greater urgency in the adoption of energy reduction measures across our commercial and industrial sectors.
Ultimately it’s a question of choice, and whether businesses are prepared to finally address the ‘Capex vs Opex’ argument and begin to enjoy the long term financial gains available through improved operational efficiency. The offer being; pay for the new equipment now, and recoup the cost through the energy savings made over its operational life. But either way, supported by the documented evidence that significant savings can be made through the correct selection and efficient operation of pumps and their related systems, the BPMA will continue its efforts to drive this clear and important message.
Further information on the work carried out by the BPMA can be found through the websitehttps://www.bpma.org.uk/ - or for any specific enquiries, please email s.smith@bpma.org.uk
The Cygnus 1 Ex Ultrasonic Thickness Gauge is a rugged, handheld, intrinsically safe instrument designed for taking thickness measurements in Zone 0 explosive atmospheres.
• Certified Intrinsically Safe to ATEX, IECEx, UKEX for Zone 0 and NRTL for Class 1, Division 1
• 3 measuring modes for corrosion, various materials and through-coat measurements
• Manual Measurement Mode allows gates and gain to be configured to suit your application
• Live A-Scans and B-scan for visual verification
• 4 quick function keys for easy control
cygnus-instruments.com • sales@cygnus-instruments.com
At the forefront of digital marketing, Engineering Update strives to bring the latest in industrial engineering in a format that provides the best usability and ease of use for its readers.
Publication Director
Jodie Little
01843 595818
jodie@jetdigitalmedia.co.uk
Editorial Assistant
Laura Sharpe
01843 448 443
laura@engineering-update.co.uk
Editorial Assistant
Leigh Little
01843 448 443
leigh@engineering-update.co.uk
Publishing House
Jet Digital Media Ltd, Suite 1 & 2 Spratling Court Offices, Spratling Street, Manston, Kent CT12 5AN
As engineering managers come under pressure to meet demanding schedules, often with fewer skilled hands and tighter budgets, the benefits of professional tool storage and management become stronger than ever.
Snap-on Industrial’s Level 5™ automated total asset management system brings order to any workplace, enabling engineers and technicians to know exactly where to find every tool they need, when they need it, saving time and easing stress.
How useful would it be if all valuable tools could be tracked from one central point? Snap-on’s Level 5™ system makes that possible. It provides complete reports on everything
managers or supervisors need to keep an eye on.
And then there’s FOD. The threat of foreign object damage is a real and present danger in many engineering workplaces. Using Snap-on Level 5™ minimises the risk of human error, as automated tool control constantly tracks every tool and detects which tools have been removed or returned, ensuring greater protection against FOD.
Engineered to track individual tools by user, without bar codes, scanners, RFID tags or other add-ons, the system works at the speed its users demand. Other systems require additional steps to scan or log activity. The Snapon system does this automatically so users save time and don’t have to depend on other steps to ensure accurate results.
Snap-on’s Level 5™ ATC boxes are network ready, using either Ethernet or wireless connection. That enables users to review activity at all Level 5 boxes in their location from one central computer, avoiding the time consuming need to inspect each box.
Major benefits of the system include:
• No individual tool scanning required;
• No RFID tags to install or replace;
• No limitations on tool size: from ¼” screwdriver bit upwards;
• Intuitive interface, with an easy to use touchscreen
• Audible voice announcement of tool removal and replacement
• Automatic locking for maximum security
• Errors announced and displayed to indicate incorrect tool position or advise when a drawer is not closed.
Says Richard Packham, Director UK & Europe for Snap-on Industrial: “Snapon’s automated system takes asset management to an entirely new level. The ability to monitor several boxes from one central computer offers a huge advantage to engineering managers.”
For technical information visit: www.snapon-industrial.co.uk; call (01536) 413904 or e-mail:
ukindustrialmarketing@snapon.com
Wolf Safety have introduced a powerful new range of ATEX certified LED installed lighting, designed for permanent use in potentially explosive atmospheres.
The world’s leading manufacturer of portable and temporary ATEX and IECEx certified hazardous area safety lighting, Wolf have been keeping people safe for more than 110 years.
The company’s designers and production engineers have now brought their vast knowledge and expertise to bear on a new range of highly effective LED installed lighting, which is safe to use in Zones 1 and 21 hazardous areas.
The range includes:
• Linear luminaires featuring the new, revolutionary Directional Linear Optics (DLO) or standard Forward Facing Array LED configurations (with battery back-up emergency versions also available);
• Floodlights with a market leading maximum light output of up to 25,932 lumens;
• Bulkhead lighting, also featuring DLO (with battery back-up emergency versions also available);
• High bay lighting.
DLO directs light exactly where it’s needed and is ideal for use in specific, close-up workspaces, reducing glare to avoid people being ‘blinded’ by the emitted light, while its excellent colour definition facilitates safety critical hazardous area tasks.
Forward Facing Array (FFA) technology can be preferable for safely illuminating large hazardous areas which need wide, even and bright light coverage, where lights are mounted away from people or at heights where glare and intensity can’t have an adverse effect on the working environment.
Says Miles Jackson, Wolf Safety’s Sales and Marketing Director:
“We know that users of Wolf products trust us to keep them safe, especially when they need to work in highly volatile atmospheres and other hazardous workplaces.
“All the values people expect from Wolf - and are seen in our portable and temporary lighting ranges - can now be found in this new installed lighting range, which we are proud to introduce.”
For detailed technical information visit: www.wolfsafety.com
Fully compliant with British Retail Consortium, HACCP and GFSI food safety standards, the Fortress all-in-one Retail-Spec Conveyor comprises numerous future-proof features. Among them ARM microprocessing power and state-of-the-art infeed, outfeed and reject sensors.
As many Fortress customers testify, purchasing a conveyor system with fully integrated technology, including retailer Codes of Practice (COP), is a failsafe way of ensuring that the metal detector will function at peak performance levels and meet retailers current and future stringent inspection performance requirements.
Sticking to its Simple to Use; Smart under the hood engineering principles, the Fortress Retail Spec Conveyor is equivocally less about conveyor belt size or configuration, but more linked to the placement of smart sensors confirms sales manager Jaison Anand.
Describing the sensors as the brains of the retailer-ready metal detector, Jaison expands: “In our experience, food processors can feel overwhelmed by the breadth of inspection technology choices. Built to a higher retailer’s Food standards, the rationale for creating our Retailer Spec Conveyor was to address this minefield and provide customers with future-proof functionality.” Fortress intentionally uses this particular retailer’s food safety standards as the benchmark, as they are the most stringent, affirms Jaison.
Machine sensors feature at every step of the inspection process. As packs
travel into a Fortress metal detector, the infeed sensor registers its presence. If there’s no contamination trigger, the outfeed sensor identifies the pack leaving the metal detector, while the reject sensor will track the placement of potentially contaminated product into the BRC-approved bins. “It’s a seamless and failsafe process that uses our Contact software to register every sensor activity, fault fix and signal in parallel,” confirms Jaison.
All these simultaneous activities are only possible with ARM Processing. “The true benefit of ARM Processing comes from being able to run multiple inspection processes within milliseconds of each other, without missing a beat. This is done with the highest precision, while also capturing and storing valuable processing data for traceability.”
For nut specialist Trigon Snacks, opting for a Fortress Stealth supermarketspec conveyor metal detector fulfilled the company’s every inspection requirement. Retailer COPs specified that as ‘naked nuts’ the company’s honey-coated range must be inspected for metal contaminants prior to own-label packaging. Additionally,
Trigon required a customised retailer specification metal detector that was sensitive enough to adapt to the fine oil and sugar tolerances.
Retailer COP revisions, although infrequent, can be a major headache for food processors and machinery manufacturers alike. To navigate these future unknowns, Fortress offers a simple and cost effective route to adhere to evolving compliance and fault warning risks.
In order to minimise business interruption, software upgrades can usually be performed as part of a validation or routine maintenance visit. From a continuity perspective, the menu and functional set up will typically look and feel exactly the same.
For smarter machine monitoring and to support supply-chain traceability, the company’s suite of Contact software offers simple yet effective data capture. Now including Contact 4.0 for remote monitoring of multiple metal detectors within the network, this software helps manufacturers
to maintain HACCP compliance and traceable quality assurance recordkeeping. Features include event logging, data collection and on-demand reports. All this data is collated from information captured by the three machine sensors. Reports can be downloaded and exported via the USB located next to the HMI.
Comparing the costs of purchasing a new machine versus a Fortress upgrade, Jaison remarks: “You are typically looking at several hundred rather than tens of thousands of pounds buying new inspection kit. Most importantly for fast-paced food processing environments, compliance can be instant.”
Jaison highlights that realistically changes to COPs focus on fail safes and addressing any machine misuse loopholes. There haven’t been any significant revisions assures Jaison for nearly seven years. “Nevertheless, we never take our eye off the ball. As soon as a new quality control or COP feature is added, Fortress R&D can be trusted to be on the upgrade case.”
www.fortresstechnology.co.uk
OMRON, a leading provider of industrial automation solutions, has announced the launch of its new OMRON TM20 cobot with a payload of 20 kg. The new cobot is ideal for tasks such as palletizing, machine tending and material handling. Whilst managing heavy payloads, the OMRON TM20 has a small footprint and a reach of 1,3 meters.
The OMRON TM20 is the latest addition to the OMRON family of TM cobots, which are known for their ease of use, reliability, and safety. It is designed to work seamlessly with other OMRON products, including sensors, controllers, and software, to provide a comprehensive automation solution for industrial customers.
One of the key features of the OMRON TM20 is its lightweight design, weighing in at just 33 kg. This makes it easy to integrate with mobile robots, providing greater flexibility and efficiency in industrial environments. The robot also comes equipped with special joint covers to protect it from cutting oil and other hazardous materials, making it suitable for use in machine tending applications.
“We are excited to launch the OMRON TM20, which expands the capabilities of our cobot family and gives customers the ability to automate heavy payload applications,” Fernando Vaquerizo, Fixed and Cobots Product Marketing
Manager at OMRON Europe. “The OMRON TM20 is designed to be easy to use, reliable and safe. It relieves operators from tasks that involve heavy lifting, while working safely side by side with people.”
OMRON’s ROI calculator supports companies in the process of evaluating an investment in collaborative robots, including easy and affordable leasing opportunities. In addition, OMRON offers a wide range of support services, including installation, training, and maintenance, to ensure customers get the most out of their investment.
Key features and benefits:
• 20 kg payload capacity for handling heavier parts and materials
• Reach of 1300mm ideal for palletizing applications
• Cycle improvements thanks to faster joints
• 24 months warranty after registration
The OMRON TM20 collaborative robot is available for pre-orders now. For more information on the OMRON TM20 and other OMRON cobots, please visit the company’s website at http://industrial.omron.eu/cobots
Taking place from 9 - 11 May 2023 at the NEC, in Birmingham, Railtex 2023 offers a unique opportunity to experience state of the art equipment and innovative systems and solutions. The show will include live demonstrations, as well as an extensive seminar programme focusing on hot-button topics for the rail industry, such as sustainability, digitalisation, maintenance and passenger experience, alongside the well-established On-Track Display area.
The UK’s railway sector has embarked on a transformational journey, in tandem with the UK Government’s aims to create a greener and more sustainable rail industry. Railtex is the ideal platform for the whole railway industry to meet under one roof and to experience products and equipment in action.
For more than 25 years, Railtex has been the UK’s showcase event for the rail industry and it continues to reunite all stakeholders of the rail sector and its key players, including rail operators, infrastructure authorities, vehicle builders, suppliers, rail transport policymakers and planners. Despite the challenging times the industry has been facing over the past two years, Railtex confirms to be a trusted industry event, playing a crucial role in companies’ recovery strategies in the aftermath of the pandemic. Railtex attracts high-profile visitors with decision-making power, from management, engineering, planning and technical design backgrounds looking for innovative solutions for all areas of the railway supply chain. Its visitors come from all key industry sectors, including main line passenger and rail freight operators, rail regulation and safety bodies, infrastructure contracting and maintenance, national, regional and local government transport agencies, and many more. Visiting companies at the previous edition included ALSTOM, Avanti West Coast, Bombardier Rolling Stock, East Midlands Railway, High Speed 2, Hitachi, London Underground, Mott MacDonald Ltd, Network Rail, Siemens Mobility Ltd, Transport for London, West Midland Trains and many more.
Numerous exhibitors have renewed their attendance for the upcoming edition, testifying the influence of Railtex in the UK rail market; Stadler Rail, EAO Ltd., Tidyco Ltd., CRRC Corporation, Prysmian Cables & Systems, Frauscher Sensor Technology, Hayley Group Ltd. and many more will be showcasing their products. You can see the list of exhibitors on the website.
Railtex provides an excellent opportunity to rekindle contacts and will bring prominent industry experts, stakeholders, and decision-makers in attendance, along with the exhibitor presentations and an extensive conference programme. Seminars and conferences hosted by high-level industry experts and speakers are in the programme which will be organised by the main show partner RIA, the Railway Industry Association. The extensive supporting programme will provide valuable insights into future trends in railway technology and will feature a broad range of topics and sessions to address key challenges and opportunities facing the rail industry in the coming years.
One of the show’s recurring features also includes the On-Track Display: an area that will enable suppliers of railmounted vehicles and track-related equipment to display their products on a real section of track. Leading track products supplier British Steel is the sponsor of the OnTrack Display.
The visitor registration is now open https://www.railtex.co.uk/en-gb/visit.html
ratio from these devices has been widely proven to enable metering of extremely low flows with great precision. The Atrato® line of patented ultrasonic inline flowmeters consists of four models operating over a flow range of 2ml per minute up to 20 litres per minute. These low flow ultrasonic flow sensors also offer excellent turndown (> 200:1), repeatability (to ±0.1%), linearity and accuracy of better than ±1.0% of reading.
As a specialist liquid flow meter manufacturer, Titan first began developing a viable, accurate ultrasonic non-invasive small bore measuring device in 2001 as part of a long-term strategic plan. The work resulted in patented ultrasonic technology which has since led to an expanding line of ultrasonic flowmeters and patents ranging from signal processing methodology to novel mechanical design.
Titan’s ultrasonic flow sensors use high frequency sound waves to measure flow using the time-of-flight principle within the liquid in a small pipe. The ultrasound is injected with the direction of flow into the liquid by one piezoelectric crystal (the sensor) and is received by a second piezoelectric crystal further down the tube. These crystals then reverse the direction of the ultrasound in the tube and both time-of-flight acoustic signals are measured. As one sound pulse is accelerated by the velocity of the liquid and the second retarded, the difference in the flight time is twice the fluid velocity, and as the dimensions of the flowmeter tubes are known the volumetric flow can be calculated.
Most ultrasonic flowmeters can reliably measure fluids that transmit ultrasonic sound waves within a band (e.g. ±30%) around the speed of sound in water at 20°C. But if a fluid has significantly differing acoustic characteristics, for instance viscous organic fluids or if measurement is at elevated temperatures, then the acoustic operational window can be missed by the sensors. Titan’s proprietary Interface Software offered on the Atrato® and MetraFlow® overcomes this application challenge. The software functionality allows you to view the Acoustic signal of the measured fluid in real time and if required, move its position in the measurement window to ensure reliable flow measurement in the conditions of operation. This increases the versatility of a single fluid calibrated meter to a much wider range of applications.
Ultrasonic flowmeters are the ideal solution for measuring low flow rates. Titan has developed several generations of ultrasonic low flow meters based upon their patented time-of-flight design able to measure the velocity of the fluid within the pipe. The very high signal to noise
Titan’s ultrasonic flow devices are independent of Reynolds numbers and can therefore operate from laminar flow through to turbulent flow. This makes them highly commercial being able to accurately measure liquids ranging from water to high viscosity oils. Being through-flow devices, they can also be tolerant to impurities in the system which would cause havoc to meters with moving parts.
The rugged, clean bore construction of the Atrato® and MetraFlow® ultrasonic flowmeters make these devices ideal for almost any low flow application, from research and development to industrial processes, and even metering of chemically challenging liquids. In addition, the Process Atrato®, durably constructed from 316 stainless steel and PEEK, and incorporating Titan’s patented time-of-flight ultrasonic flowmeter technology , is specifically designed for use in demanding process and control environments.
To discuss an optimised flow measurement device for your OEM application please contact Titan Enterprises on +44 (0)1935 812790 or email sales@flowmeters.co.uk Or visit our website for further information.
Titan Enterprises has recently been granted additional patents for its ultrasonic flow technology used within their range of Atrato®, MetraFlow® and Process Atrato® flow meters.
Oil and Gas High Temperature
The Cygnus 6+ Pro Ultrasonic Thickness Gauge boasts a full range of useful features for professional users, including A-scan, B-scan and comprehensive data logging.
Multiple-Echo mode for accurate, through-coat measurements as specified by Classification Societies
Echo-Echo and Single-Echo modes for heavily corroded metals with a thin or no coating
Facilitates high temperature measurements on hot materials without shutdown or isolation
Live A-Scans and B-scan for visual verification
Advanced data logging for easy reporting and analysis
cygnus-instruments.com • sales@cygnus-instruments.com
Ewellix, the leading global innovator and manufacturer of advanced linear motion technologies, has developed a package of modular lifting column platforms developed specifically for medical applications. In particular, they are designed for use with patient tables, ceiling stands and wall/ floor units in X-ray suites and other medical imaging modalities.
The new products include lifting columns and sophisticated control units based on the company’s innovative SmartX digital technology. The focus is on creating products that are robust, smooth, low noise and ergonomic for healthcare professionals, while being modular, and engineered to the highest quality to simplify the design and assembly process by medical device OEMs.
One of the challenges for X-ray departments is positioning relatively heavy X-ray tube heads or detector systems, which are often mounted on overhead or wall/floor frames. Each head or detector system can typically weigh up to 50kg, yet has to be moved easily and precisely to target the appropriate area of the patient’s body.
The solution developed by Ewellix is based on its patented ‘Effortless Technology’. This eliminates the traditional approach where counterweights are used to balance the head or the detector. Instead, the Ewellix system incorporates an intelligent 5-stage lifting column fitted with servo motors and a force sensing unit. Controlled as part of the SmartX digital platform, this modular construction allows the X-ray head or detector to be moved at speed – up to two metres in a few seconds with the lightest touch from an operator. The speed and strength of force applied by the user is automatically detected by the force sensing unit and then converted into a linear motion under precise control from the SmartX software.
The lifting column is capable at moving at speeds of up 600mm/sec, yet provides exceptionally smooth and silent operation. Digital communication in combination with the SmartX controller enables precise synchronised motion of
Thanks to the Drive Assisted Motion (X-Motion) in the fivestage lifting column, users can move and position ceiling- or wallmounted X-ray tubes effortlessly. The lifting column extends from floor level to head height in two to three seconds without the operator even noticing that he is moving 50 kilograms.
the X-ray tube and the detector. The synchronised motion can be controlled automatically by the X-ray suite control system or by user input on the force sensing unit of the X-ray tube or the detector.
Use of individual force sensing units and position detection sensors for each lifting column and the SmartX digital controller constantly cross-reference the sensor outputs, ensuring that the movement of the X-ray tube and detector is precisely and safely regulated.
Also included in the new package for medical applications is the smart TLT series of lifting columns equipped with an integrated SmartX controller and absolute position encoder. These are robust, fast and powerful, being fitted with two DC motors that are capable of providing a lifting force of up to 5’000N. The TLT series also has a low, torsion-resistant profile and compact design that minimises the overall dimensions of each unit, at both maximum and minimum extension. The design and construction of each TLT unit enables them to be used for heavy and off-centre loads. With the built-in smart controller, the TLT lifting columns provide a digital communication interface and advanced position and speed control. Precise synchronised motion, soft start and stop and safety features like anti-pinching detection makes it a perfect lifting column for X-ray patient tables.
The complement of the new medical devices is made up of high-performance modular profile-rail LLT guides. These precision devices provide smooth, load-bearing guides for use with, for example, adjusting the X-ray tabletop in the X- and Y-axis. Ewellix offers a wide choice of sizes, lengths and rail and carriage options.
SmartX telescopic columns are also used for the synchronised patient table. The two TLT columns are synchronised by a SmartX controller integrated into each lifting column, which communicates with each other via a digital bus system. This ensures that the two TLTs retract and extend in parallel and evenly under all circumstances.
The new medical package for X-ray and medical imaging systems is backed by Ewellix’s global network of technical and applications support, with the addition of custom design and engineering services for medical device OEMs.
TR Fastenings and TENTE Castors, a leading international castor and wheel manufacturer, are working together to enhance TR’s already extensive sheet metal range.
The existing product range included on the TR website, has been enhanced with more than 150 new products. TR is now able to provide mobility solutions to a wide range of customers and applications from domestic furniture and laundry carts to hospital equipment and heavy duty industrial.
New products will include Swivel Braked Castors, Swivel Castors and Fixed Castors with accessories such as Circlip Stems, Stem Plates and Threaded Stems. Wheel diameters are available from 14mm to 200mm, serving a wide range of applications.
TENTE were attracted to working with TR to access and supply to their wide customer base in sectors such as health and home, energy, tech & infrastructure and general industrial
Produced in high-quality materials, including solid rubber or synthetic compounds, this range of Castors is not only designed to be aesthetically pleasing but have longevity and increasing whole-life efficiencies.
Further product features include load capacities ranging from 25kg up to 1,200kg and a wide variety of wheel tread options to suit different situations including: Polyurethane, Polypropylene, Polyamide, Thermoplastic Rubber, Solid Rubber and Elastic Rubber Tread.
Sean Cushen, Commodity Manager, TR Fastenings, said: “Following on from the successful launch of our Enclosure Hardware products, this was a natural progression to add the
TENTE range. Having spent time with the TENTE technical and manufacturing teams on site, we have got to know the brand and we are confident that we can work very closely together.”
Carl Garner, Managing Director, TENTE Castors Ltd, said: “TR Fastenings is a global company with a respected reputation in servicing and supplying a wide range of products in many fields of applications and TENTE is a global manufacturer with a wide range of castors and wheels to suit all industries needing the right mobility solution for all their customers.
“It was clear from an early stage, when I spoke with Glenda Roberts, TR Global Projects and Marketing Director at an exhibition and Sean Cushen at a networking event, that our two companies share many values and are passionate about exceeding customer expectations. We are now at the stage where both our companies can grow together through our teams and our brand.”
www.trfastenings.com
In this article, Fulton’s Leigh Bryan looks at the strategies available to lessen the impact of boiler plant downtime and breakdowns and considers the impact of national and global supply chain issues.
Ask any engineer what the ideal steam boiler setup is to cover breakdowns and scheduled maintenance and they’ll tell you it’s simple, employ an N+1 (spare boiler) strategy, where you always have one boiler available as a spare to operate as backup.
However, this is not always practical. Common reasons include footprint issues, where there just isn’t enough room available to fit the extra equipment into the plantroom; or a financial decision when, by tying up capital in a ‘spare’ piece of equipment, those funds could be used elsewhere in the business.
Whatever the reason and no matter how well the boilers are maintained, the likelihood is that at some point there will be an occasion where a boiler breaks down. It could be a perishable item such as a gasket or sight glass that fails, or other components incorporated into the boiler pressure vessel including level probes or steam/water valves. Of course, good, accurate water treatment and correct load matching to the boiler help prevent failures that occur from corrosion or erosion, but they cannot be completely prevented.
Then there are the wear and tear items including motors and their actuators or switch gear; manual and automatic valves where packings and seals will gradually perish; ignition probes and ionisation rods that eventually burn
away; and reactive components such as UV cells that degrade with time.
And let’s not forget recent global supply chain issues, which have seen almost all products impacted by extended lead times, with some not just increasing by days, but weeks or even months. It is therefore worth taking into consideration the spares kept on site, as supply of the most basic components are also being affected and may not be available exstock or at short notice.
So where does this all leave the customer? In an ideal world – supported by the Original Equipment Manufacturer – while companies including Fulton are doing their best to hold relevant stock, they are still like everyone else, subject to delays in obtaining raw materials and parts to replenish their own stock levels.
Even if items are held in stock, there is the delay in getting it to the customer, which generally means a lead time of 24h hours on an overnight delivery and sometimes 48h to remote locations. So even if you only consider the timeframe from the point of diagnosis of a known fault, to the part or parts arriving at your facility and being installed, these delays to production, or temporary closures of facilities due to steam being unavailable for the processes, are costing facilities dearly in downtime and lost production for the sake of a relevant spare part.
So, if you’re not operating an N+1 strategy and don’t have that spare boiler in place, holding your own spares is of vital importance to ensure overall equipment and process efficiency.
At Fulton, we help clients make that informed decision. With our product and industry knowledge, we produce full spares lists for our own heat transfer solutions and even those of other OEM steam boilers, but rather than leave it there, we identify components that are considered ‘highly-recommended’ due to a higher risk of failure or long lead times. We simplify this further with a traffic light system that highlights, from green to red, the criticality of a particular spare part. By keeping it simple yet effective, it allows our clients to make informed decisions, selecting the most relevant equipment for their site held spares and working on a package to suit their budget.
On those occasions where clients look at the risk and possible financial implications and chooses to hold a full spares package, Fulton recognises that everyone is in the same current global economic situation together and acknowledges our client’s foresight by providing good discounts to lessen the fiscal impact to their business.
There really is only one way we all come out of this economic squeeze in one piece, and that’s by working together. Maybe it’s time to re-evaluate the N+1 philosophy, and to recognise Fulton can be that +1 to your boilers and your business.
For further information please visit www.fulton.co.uk.
The Manufacturing Institute (TMI) has been trusted in delivering high-quality and impactful training since 1994. Offering courses that create impactful changes to a business such as Six Sigma, Lean Manufacturing, and Team Leadership. This year has started off with a bang for TMI, receiving City & Guilds assurance for the Team Leadership Development Programme (TLDP) and the Accelerated Route to Lean Manufacturing (ARTL). These are often the gateway onto the MSc in Manufacturing Leadership, or even larger continuous improvement consultancy projects and Shingo.
The City & Guilds Assured Benchmark is a quality assurance framework, which evaluates eight areas of programme design and delivery. It is the Benchmark Standard to confirm that an organisation has met the global quality standard set by City & Guilds. Lisa Riley, Executive Director at TMI reflected, “These programmes are so enduring that customers old and new refer to them by their acronyms. In the last 12-months, both programmes have been updated and refreshed. It felt like time to get them formally ratified by one of the Nation’s most familiar educational organisations – City & Guilds.”
Joe Bell, Strategic Commercial Manager at City & Guilds said, “City & Guilds is delighted to be able to work with organisations who value good quality skills development. The Manufacturing Institute has invested in developing these programmes to achieve the City & Guilds Assured benchmarks, which now evidences that the courses meet world-class quality standards on all aspects from planning and design, to delivery and evaluation. Congratulations TMI!”.
These programmes help build a coaching culture, giving employees the opportunity of personal development, which reflects on their business. TMI understands this culture and encourages delegates to continuously develop. Upon successful completion of the Programme, delegates receive a co-branded digital credential highlighting their personal development, which includes detailed information about the learner’s skills and achievements.
For more information about Leadership and Lean training, please visit www.manufacrutinginstitute.co.uk or telephone +44 (0)161 245 4845 for a prospectus.
With the GSME and HOTSPOT detectors from REMBE, an artificial intelligence has been created that detects fire and explosion events at an early stage. The GSME detector is an artificial nose, "trained" for pyrolysis - popularly known as smoldering gases, while the HOTSPOT detector represents an artificial eye that already detects surface temperature changes of 1 °C.
REMBE´s HOTSPOT X20 measures surface temperatures using an intelligent evaluation system, which divides the field of view into detection zones. A separate temperature threshold value can be set for each individual zone in order to tailor the detection to the process as far as possible. The HOTSPOT X20 can even identify small temperature increases (1 °C) and enables to warn the operator of a fire or glowing embers at extremely early stages. The HOTSPOT X20 can also be used in explosion atmosphere up to zone 20 and under high dust loads and monitors a temperature range in the standard version of 0-200 °C (higher temperatures possible, but typically not required).
Mainly hydrocarbon compounds are released when many substances thermally decompose. If there is incomplete burning without a flame and a low oxygen supply, carbon monoxide is created as well. The GSME X20 pyrolysis gas detector, for instance, has been designed for detecting these gases, even as they develop. Alongside carbon monoxide and hydrocarbon compounds, nitrogen oxide and hydrogen compounds (CO, HC, H2 and NOx) are also monitored. With the aid of an intelligent evaluation algorithm, a process behaviour can be ideally mapped and normal off-gasing be adopted. If a concentration increases above the usual level, the GSME X20 immediately triggers an alarm. The detector, is also suitable for explosion atmospheres up to zone 20, monitors concentration ranges from 0-100ppm.
When the location and mounting position are ideally designed in an explosion protection concept, HOTSPOT X20 and GSME X20 allow explosions and fires to be prevented through early detection.
Ethernet is being deployed across more and more areas of industry and is the connecting element for both IT and OT (Operational Technology). To enable customers to implement robust networks for industrial use, HARTING is constantly developing and refining its range of reliable Industrial Ethernet connectivity.
The miniaturised ix Industrial® connector offers users a compact and industry-compatible interface for demanding applications in the PROFINET environment. It delivers Cat. 6A performance for 1/10Gbit/s Ethernet at the control level, whilst its high current-carrying capacity supports both existing and future Power over Ethernet (PoE) applications.
HARTING have slashed the PCB jack size by a substantial 70%, enabling manufacturers to use it in much smaller devices. In addition, it combines both data transmission and power supply into a single interface, further reducing the area required for connectors within devices.
As well as significant space savings, the ix Industrial® has been specifically designed and built to withstand the rigours of industrial environments. This resolves the issues associated with the RJ45, whose plastic locking
tabs are easily broken in busy manufacturing environments, which can lead to contact problems as the connection works loose.
For awkward areas with restricted space conditions, easy installation is crucial. The M12 PushPull is the solution, offering handling, time saving and reliability benefits. M12 PushPull uses a tool-free connection technique that ensures absolute dependency and means the assembly density can be significantly increased, helping to save valuable space.
To make SPE technology accessible to further application areas, HARTING has developed a PCB terminal. Terminals simplify the connection of SPE, helping to bring Ethernet to the field level and simplify handling. This is particularly interesting within the context of SPE and IIoT, with low data rates from 10 Mbit/s and transmission lengths of up to 1km in industry, building and process automation.
There are also new variants of the T1 Industrial interface for Single Pair Ethernet. There are M12 and M8 housings, standardised according to IEC 631716, and new hybrid concepts for SPE plus Power, standardised to IEC 63171-7. These have been developed to meet power requirements beyond the possible 50W of Power over Data Line.
To learn more about the HARTING Industrial Ethernet portfolio, please visit www.harting.com/UK/en-gb/industrial-ethernet or email salesuk@harting.com.
Following yet another exhaustive Judging Session, which was held virtually on 26th January, the Finalists in the 2023 Pump Industry Awards have now been determined.
From the record number of entries received, and through some incredibly tight scoring, the Judges shortlisted 46 Finalists across the eight award categories to go through to the public vote. Those that were fortunate enough to be selected are as follows: -
Sponsored by Process Engineering
• ABB: SynRM IE5 Motor & Drive Package
• ARMSTRONG FLUID TECHNOLOGY: DEPM Single Phase Pump
• ARO: EVO SERIES™ Electric Diaphragm Pump
• BAKER HUGHES: Water Injection
Centrifugal Pump
• BROOK CROMPTON: EC Motors
• FLUX PUMPS: Viscopower
• JOHN CRANE UK: Global Standardized
Upstream Pumping Support System
• JOHN CRANE UK: MPF - Automated
Backflush High-Flow Filter
• SALAMANDER PUMPS: TapBoost
• WILO UK: Wilo-Actun ZETOS-K12
Borehole Pump
Sponsored by Stuart Turner
• ABB: Glendevon Project
• APEX PUMPS: Hindås Waterworks Project
• BAKER HUGHES: Northern Lights
CO2 Pumping Storage
• SULZER: Retrofit of Five Membrane
Feed Pumps for a Desalination Plant
Sponsored by SPP Pumps
• ABB: Glendevon Reservoir Hydroelectric Project
• AES ENGINEERING
• HAYLEY 247
• STUART TURNER: Monsoon & Showermate - Digital Installation Manual
• SUNDYNE HMD KONTRO SEALLESS PUMPS: LMV-801S
Sealless Vertical API 685 Pump
• WATER POWERED TECHNOLOGIES: The Papa Pump
• WILO UK: Wilo-Actun ZETOS-K12
Borehole Pump
Sponsored by WEG UK
• APEX PUMPS
• CREST PUMPS
• SPP PUMPS
• STUART TURNER
• WILO UK
Details of all these Finalists are now available to view on the dedicated awards website –www.pumpindustryawards.com/finalists.
An online voting process was operational until 5.00pm on Wednesday 15th February, allowing readers to vote for who they think should be the outright winner in each category. So, in tandem with the Judges, pump users have had their say in who will be presented with the Winner’s Trophies at the Gala Awards Dinner on 16th March at the Hilton at St George’s Park Hotel, Burton-on-Trent.
Places are still available at this ‘not to be missed event’ so whether it’s taking a table to host customers or booking a few seats for you, your team and partners, don’t miss this fantastic opportunity to enjoy a wonderful evening of great food, fine wine, fantastic entertainment and that all-important networking until the early hours, when our now infamous ‘survivors’ breakfast’ will be served.
Sponsored by Stuart Turner
• BPS PUMPS
• SEAL & PUMP ENGINEERING
• TOMLINSON HALL & CO.
Sponsored by Wilo
• ABB
• AESSEAL
• EMiR SOFTWARE
• JOHN CRANE UK
• SUTTON CASTINGS
• WEG (UK)
To help deliver the 22nd staging of this key industry awards ceremony, we will this year be joined by Kevin Keegan, one of the most recognisable faces in British football. An illustrious playing career included time at Liverpool, Hamburg, Southampton and Newcastle as well as the national side, captaining England for six years until his international retirement after the 1982 World Cup. As a manager he held the reins at Newcastle, Fulham, Manchester City and England.
Places can be booked online at www.pumpindustryawards.com/book-tickets, and with a record number of tables booked already, it’s looking to be a great event.
Sponsored by Crest Pumps
• ADC ELECTRICAL: ADC Pump Services Division
• AEMT: Ex Repair Course
• AESSEAL
• CDR PUMPS: Fundamentals of Pump Training
• KIWA WATERTEC: Water Regulation 4 Compliance and Certification
• SULZER: Sulzer Academy for Pumps and Systems
• WILO UK
Sponsored by World Pumps
• Sam Kemp, APEX PUMPS
• Josh Bottomley, EMiR SOFTWARE
• Lewis Wilkes, SALAMANDER PUMPS
• Jack Linley, SULZER
Classroom based “Live” webinars
On-site courses
Tailored options
For more information call 0121 601 6691 scan code for the training guide or email: training@bpma.org.uk
Fluid transfer products for upstream, downstream and refining
• Global inventory and locations
• Sales and technical support worldwide
• In-house engineering & design
• ISO 9001 accredited
• Pressure Equipment Directive
Products:
• Hoses and hose assemblies
• Hose & pipe fittings
• No-spill couplings
• Safety breakaway fittings
• Blow-Out prevention couplings
• Hydraulic Fracturing: Low Pressure Systems
• Loading arms
• Liquid level sensing
• Zero emission valves
Advantech, a leading provider of AIoT platforms and services, is pleased to launch its ARK-7060 extreme high-performance edge computer, which brings server-class computing capabilities, flexible expansion, rich storage capacity, and high network bandwidth to the edge.
Advantech’s ARK-7060 is an extreme high-performance edge computer with multiple expansion slots and fast data transfer speeds that empower edge data servers, AOI visual inspection, and AI vision equipment applications. It is equipped with Intel® Xeon® D-1700 series processors up to 10 cores at 67W and 4 x DDR4 SODIMM sockets that support up to 128 GB. ARK-7060 offers 2 x GbE, 4 x USB 3.0, 4 x COM ports for diverse device connections.
ARK-7060 provides expansion slots for PCI, PCIe x4, and PCIe x16. Its PCIe x16 slots can support graphic cards up to 350W such as NVIDIA RTX Quadro A4500 and A5000. These highend graphic cards require adequate power supply and at the same time may overheat as they try to complete intense tasks. The ARK-7060 system adopts advanced thermal designs to improve heat dispersion, and it also has a dedicated thermal kit for industrial fanless graphics cards. It has a built-in 850W power supply, which makes it easy for equipment integration. ARK-7060 delivers highperformance computing and can be used with motion control cards, frame grabbers, and graphics cards, which is suitable for AI visual inspection and AI vision equipment.
As factories transform into smart manufacturing, the amount of data collected keeps increasing. In order
• Intel® Xeon® D-1700 series processor
• 4 x DDR4 SO-DIMM sockets support ECC/non-ECC memory up to 128 GB
• Versatile expansion: PCI, PCIe x4, PCIe x16, M.2 B-Key, M.2 E-Key
to store and transfer a large amount of data, ARK-7060 supports up to 4 x 2.5” SATA III hard drive bays and delivers high data transfer rates via optional 10GbE ports and M.2 B-Key for 5G modules.
To enhance the security of ARK-7060, the system has dual BIOS for BIOS backup and recovery, lowering the risk of BIOS damage and protecting from potential viruses or data corruption. As for security of the OS, ARK-7060 supports TPM 2.0, and the system is bundled with McAfee for whitelisting
• 850W power supply built-in
• Supports up to 4 x 2.5″ hard drives
• Optional 2 x 10GbE Ethernet ports
• IPMI 2.0-compliant management with reliability and security enhancements
technology and Acronis for data backup and recovery. These features enhance data security and protection and give users peace of mind when managing their data within ARK7060. The ARK-7060 onboard BMC (baseboard management controller) provides IPMI 2.0 architecture for remote management, and this allows customers to realize both in-band and out-of-band control on ARK-7060. In addition, users can also remotely switch between the two BIOS through BMC. Also, ARK-7060 is bundled with WISE-DeviceOn remote management software by Advantech, thereby reducing maintenance costs and system downtime.
For customers requiring this product in a custom variant, Advantech’s European DMS team offers a wide range of local design and manufacturing services. For more information, please visit http://bit.ly/AdvantechDMS.
THE GUARDTECH GROUP have stepped up their quest to offer the most comprehensive cleanroom package around by launching an exciting new website for their CleanCube Mobile Cleanrooms brand.
The brand-new site –www.cleancube.co.uk – is the first standalone brand subsite to launch since the Guardtech Group was formed at the turn of the year.
Existing and potential future clients will still be able to access support, technical data and general information on every product and service provided by Guardtech at www.guardtech.com – but this launch marks the beginning of a series of new websites the Group will be unveiling to improve their overall customer experience.
The new CleanCube subsite is packed with useful technical information about their extensive range of portable cleanroom models, including comprehensive breakdowns of the Structural, Mechanical & Electrical and Furniture & Equipment options available for buyers.
Guardtech Group Commercial Director Mark Wheeler said: “We’re delighted to finally unveil our exciting new CleanCube website. A lot of planning, thought and attention to detail went into the development of the site.
“We’re confident all that hard work that went into creating this new platform will have a significantly positive impact in how we market and, ultimately provide, our award-winning portable labs and cleanrooms to businesses conducting exciting work all over the world.”
The subsite explains the concept behind Guardtech’s different portable cleanroom solutions, illuminating the make-up of their Mini, Midi and Maxi container models and Mobi and Mobi+ vans, as well as their newly revamped GMP, ISO and CNC internal Specifications.
The GMP Specification is the highest grade of internal fit-out that can be
selected for any CleanCube model. All internal components selected are suitable for high grade Pharmaceutical and clinical environments where attention to detail, quality of finish and reduction of ledges is critical.
ISO brings together the most appropriate combination of components to achieve an ISO 14644 classified environment. Balancing a high-quality, clean finish with a cost competitive Specification enables CleanCube ISO to meet the full spectrum of ISO 5 to 8 classification whilst ensuring value for money and time to build remain the critical factors.
CNC is designed to provide a cost-effective balance of componentry that will best suit an unclassified controlled environment, utilising materials that are specified for lower-grade cleanroom builds whilst downgrading some of the mechanical & electrical interfaces typically excluded from cleanrooms. CNC provides a high-grade laboratory finish with off-the-shelf components and plant.
Site visitors can explore the finer details of the different components on offer, picking and choosing the material grade to meet their specific end-user requirements.
Having already launched their innovative ‘online cleanroom builder’ tool – the Isopod Configurator – earlier this year, Guardtech are currently
developing a version for CleanCube to sit on the new subsite.
“We’re trying to change the game,” Mr Wheeler adds. “All of the things we’re doing are a means to improve the customer journey, while also demonstrating what an exciting, dynamic, creative and knowledgeable business we have.
“We’re absolutely convinced that this new website, and the others to come, will raise our offering to an even higher level and help us to deliver the complete cleanroom package for our clients for many years to come.”
The Group have also secured a new CleanCube manufacturing facility in Brandon, Suffolk which will give clients the opportunity to view an on-site demo unit.
Manufacturing Manager Michael Burton heads up the new premises –and he’s looking forward to welcoming new customers to CleanCube HQ.
“We’re going to have some fantastic CleanCube models in production throughout the year,” he said, “so any potential visitors are going to get the chance to see some interesting projects if they choose to come on down. We can’t wait to start hosting!”
Check out the new website at www.cleancube.co.uk – or call 0330 113 0303 or email sales@guardtech.com for more information.
Process automation, machine construction, and increasing the efficiency of systems or installations require highly precise equipment, and encoders are such equipment. The encoder is part of the automation system, thanks to which it is possible to determine the efficiency of various types of machines. With proper knowledge of encoder functionality and the ability to use them, it is possible to increase the company's productivity - in other words, encoders save time and money and improve results. The encoder allows to control of the movement, drive, and operation of individual machine components, and then - most importantly from a business perspective - to optimize operations.
Encoders are increasingly becoming the basic elements of automation systems due to their wide applicability but also the effects of their use. They are used, among others, in:
• Machine building
• Robotics
• Automation and sorting
• Aerospace
• Food & Beverage
• Printing
• Material Handling
• Mobile equipment, etc.
British Encoders Company offers two major types of encoders, linear measurement encoders, such as the TR1 Tru-Trac™ or the Linear Cable Encoder (LCE), and rotary encoders like the Model A58HE which is an EtherCAT or PROFINET-ready. Linear encoders have a read head and track.
The read head will slide along the track with a predetermined scale. This will produce an output for distance travelled typically in pulses per inch (PPI). A rotary encoder converts the angular movement of a rotational device and will have an output for rotation about the fixed axis typically in pulses per revolution (PPR). Within linear or rotary encoders there are two basic types of electrical output formats: incremental or absolute. Absolute encoders have a unique digitally coded output or address for every distinct position of the encoder. Incremental encoders will output a count or pulse at periodic predetermined intervals. Rotary incremental encoders are the most used encoders.
Encoders are indispensable wherever precise measurement and supervision of speed, the direction of travel, distance travelled, and position of mechanical elements or the number of rotations performed is necessary. In any case, the encoder invariably affects the proper and efficient functioning of machines and systems. It is therefore a small investment in great profits for enterprises.
Contact our team of experts to get your ideal motion control device.
T: +44 (0) 1978 262100
E: sales@encoder.co.uk
W: www.encoder.co.uk
Waste food is food which cannot be consumed by somebody. With large numbers of people going hungry across the globe, and increasing pressure on land, there is a moral imperative to maximise the amount of produced food which is actually consumed. Food production is also a significant source of global GHGs, and waste food generates further emissions without any nutritional benefit. Reducing food waste is a key factor to mitigate climate change.
By Matt Hale, International Sales &According to some estimates, over a third of all the food produced globally is wasted. The UK generates around 9.5 million tonnes of food waste a year, of which some 1.5 million tonnes (16%) comes from manufacturing
1. While not all of this material is edible, in terms of efficiency and reducing greenhouse gas (GHG) emissions, prevention of this waste is preferable to other methods such as food redistribution or use as animal feed, or recycling, energy generation or disposal via anaerobic digestion, composting, incineration or landfill.
Waste food also has significant financial costs for businesses. Not only does the raw material have a cost, but additional costs are associated with the redistribution or disposal of waste food products. As food and energy costs have undergone massive inflation over the last 12-18 months, the need to control costs and maximise utilisation of expensive ingredients has also increased.
There are a number of approaches which businesses can use to assess and reduce food waste, and in most cases a mixture of valorisation, utilisation and process improvement (or implementing LEAN processes) will be required.
Some key areas to consider include:
Good quality packaging improves the shelf life of food and therefore reduces waste in the distribution chain and in households. However, there is increasingly a balance between reducing the use of plastics and non-recyclable materials, while increasing product shelf life (wrapping cucumbers in plastic is a classic example).
Choosing the right packaging during the manufacturing process can improve shelf life and reduce handling, improving efficiencies and reducing waste. Accurate and consistent weighing is also important, as even a few grams surplus in each pack can quickly add up to large sums of money.
Inaccurate forecasting can mean you waste raw materials and ingredients. Don’t assume that you need to produce a certain number of products unless you have clear evidence for such demand (such as agreed orders or demand modelling). Ordering enough ingredients to produce a certain volume of product but actually producing less, is one of the biggest sources of waste in food businesses, particularly when using fresh or perishable ingredients.
Better and more accurate forecasting models allow you to guess less and maximise the use of ingredients.
Without measuring waste, you can’t tell if you are reducing it, or adequately calculate what it is costing you. Feeding this data into companywide systems so that it can be analysed centrally helps to identify areas of inefficiency and waste, allowing manufacturers to streamline processes and reduce waste.
Having systems in place to measure waste and efficiently plan production can greatly reduce the amount of waste generated. For example, producing subsequent or similar batches of product may reduce the need to empty processing lines between production runs.
Quality control is vital to maintain standards and food safety, but there is a need to avoid overzealous standards which may result in ingredients which are perfectly usable being discarded. Likewise, under- or overcooking-food, or having unnecessary trimmings or off-cuts results in unnecessary waste.
As well as making sure that the quality standards and specifications being applied are appropriate for the product, it is also important to make sure that the processes used for quality assurance are operating correctly, whether that is calibrating equipment or training staff.
As with other areas, staff awareness, education and involvement play a huge role in minimising waste. Employees should be invested and committed to reducing waste and building it into company culture.
As well as educating staff about the impacts of waste, they should be encouraged to take part in a full dialogue as employees often have useful insights into the manufacturing processes. Recognising and rewarding innovative ideas can help waste prevention become an ingrained habit and a key value within the organisation.
Even with the best will in the world, some ‘waste’ is likely to be generated. This should be dealt with in a way which maximises its usefulness or value. According to the food waste hierarchy, in order of preference these disposal options are:
a. Redistribution to people
b. Use for animal feed
c. Anaerobic digestion
d. Composting
e. Incineration with energy recovery
f. Incineration,
It may also be possible to utilise certain products in novel ways, for example vegetable oils and animal byproducts (ABPs) can be converted into biodiesel where facilities allow.
New technology or equipment may help increase utilisation, for example by recovering more usable protein from meat carcases. Another option is to optimise existing production processes, particularly when it comes to production changes or cleaning-inplace (CIP).
Depending on the product, such cleaning is handled and product complexity this may be required several times a day between production batches. If product remaining in equipment is ‘flushed’ using pigging systems, large quantities of otherwise usable product could be lost. Careful product design can also recover product. For example, the HRS R Series of heat exchangers uses a scraper bar within the inner tube to enhance product flow, prevent fouling and minimise pressure drop. It has the unique feature is that when configured correctly, the unit can be run in reverse, effectively emptying the heat exchanger tube(s) of product without damaging it or changing its characteristics, so it can be recovered and utilised.
Due to the amount of product saved, and the fact that it is often unnecessary to install additional product recovery systems, the R Series heat exchanger can quickly pay for itself, and in the long term can be a more economic option than alternative systems which have lower capital costs. www.hrs-heatexchangers.com
Consider how you dispose of unavoidable waste. For example, anaerobic digestion is preferable to landfill