Suitable virtually to any environment, application and industry Concept workbench

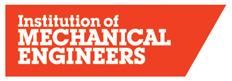
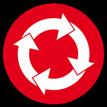
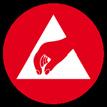
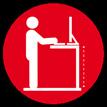
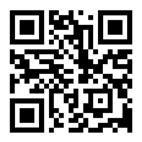
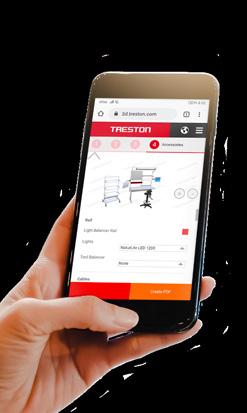
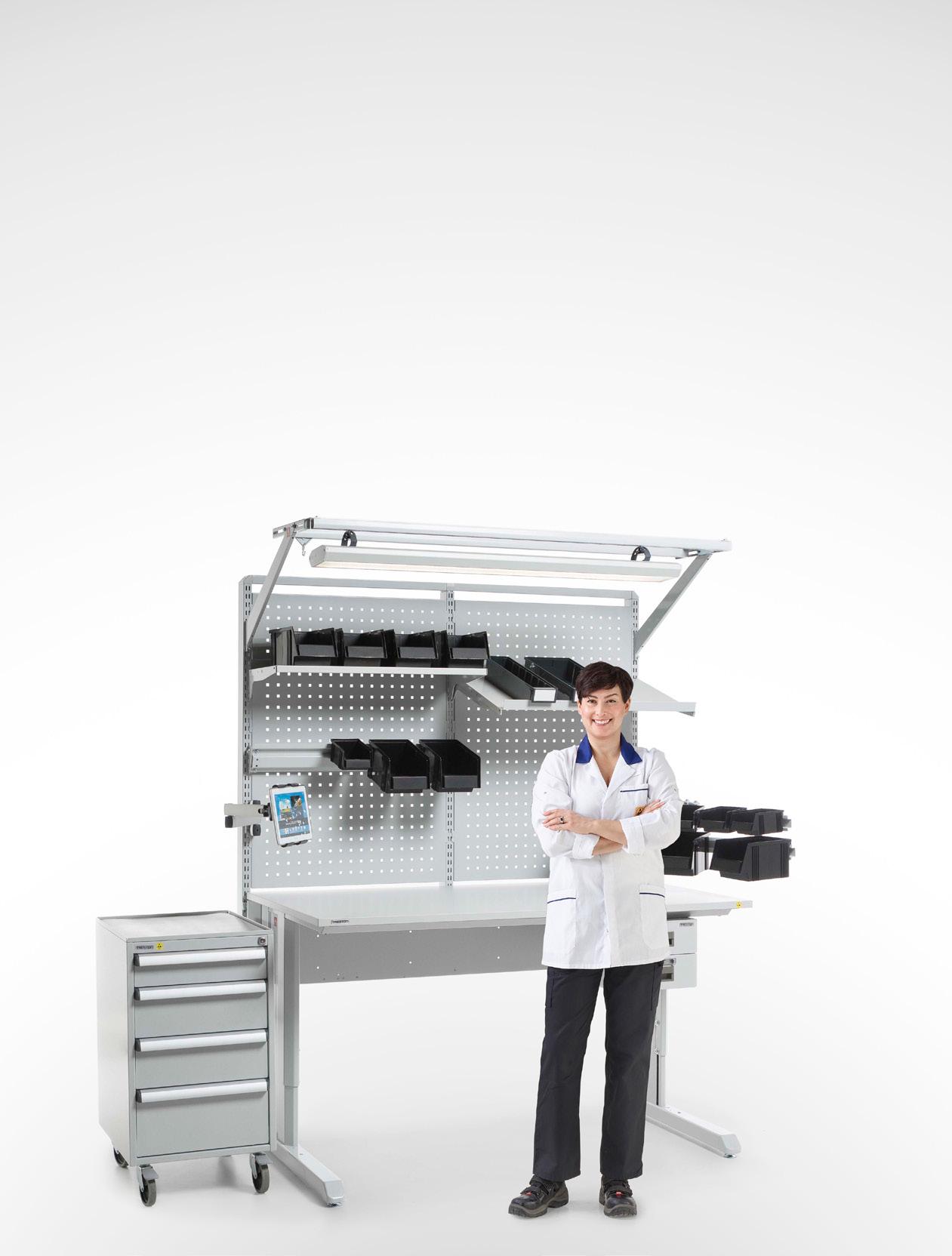
Suitable virtually to any environment, application and industry Concept workbench
Titan
By investing in research and development and continually pushing the boundaries of technology – and running down a few rabbit holes along the way – Titan maintains its competitive edge in the flowmeter market.
Titans’ focus for R&D is achieving a solution for our OEM customers, driven by flow technology. This can take the form of:
1. Product portfolio development: such as identifying where products can be improved as Titan has recently achieved with the launch of the new Pulsite® Link pulse & analog converter.
2. Breakout R&D: Exploring a new market focus or application such as developing a low-cost ultrasonic flow measuring device utilising our technology.
3. Customer / OEM bespoke product development to be incorporated into a customer’s specific application.
The R&D creative process is generally sparked by a customer who presents a problem that the development team can progress and investigate workable solutions. Development routes can also derive from a ‘Eureka’ moment, a mistake (3Ms post-it notes come to mind) or where we feel the market is going – driven by emerging technology.
Neil Hannay, Senior Development Engineer with Titan Enterprises, explains: “OEM customers come to us with a problem or need and we scope out a bespoke design concept that has the potential to solve this.”
In forming the initial concept designs, close working with the customer to develop specific design parameters and
overcoming fundamental difficulties that may be encountered is key from the outset. Understanding what the priority is for the customer is also essential at this early stage as it will influence the development route and technology used within the concept design process. In the simplest terms, is the customer prioritising accuracy over product costs, or looking for a low-cost solution with reliable performance?
Defining a more comprehensive design specification will enable concept models of designs to be composed that meet both Titan’s performance specifications and the customer’s process or system.
Working with a drinks dispenser OEM, the design brief needed to consider:
• Dimensions to fit within the limited physical space available
• Dual fluids – a single unit being able to measure both non-viscous and viscous liquids side by side
• Specific connections to fit existing equipment
• Use of approved (NSF/FDA) food grade materials
• Cost and production window
Once the concept designs are agreed, the next phase is to agree pricing of the tooling and final meter, based on expected production quantities. For Titan, typically our OEM customers invest in the injection moulded tooling which is bespoke for them and they ultimately own this; the design remains within Titan’s intellectual property.
Machined prototypes are put through a rigorous in-house testing process for design and performance before being issued to the OEM to test in-situ. “This allows us to uncover any unexpected issues - or indeed cause unexpected issues!” says Neil. “We often find ourselves doing lots of ‘head scratching’ in the testing phase and it’s where the team’s problem-solving skills come into their own,” Neil continues.
For example, a recent machined prototype unit in test was below its expected performance. Several rounds of rebuilding followed, from gears to
body parts, but the performance of the meter was still erratic. Two crucial aspects were discovered:
1. The surface finish of the machined body was not good enough for the oval gears to freely rotate so friction lowered performance.
2. The softer material of the unit was fractionally distorted when clamped in the calibration rig, causing a minor impedance of the gear rotation which constricted the flow.
The prototype here was reworked using a harder material and polishing the internal surface, resolving the performance issues identified.
The prototype is sent to the customer to test in situ and verify both the meter’s physical and mechanical performance meets their requirements in all operational situations. Any modifications to dimensions for example, or adjustments to fittings within the system are worked into the final design. This iterative process of finalising design requires close working with OEM customers, including reevaluating costings and agreeing production volumes.
Titan’s flow meters are typically incorporated into much larger industrial systems where accurate, reliable recording or control are required. Neil concludes: “Investing in R&D is paramount to us staying ahead of the game and taking advantage of the latest technologies, and our R&D spend is more than three times the industry average.” A team that combines suitable training and commercial experience, market awareness, problem solving skills and a creative spark enables Titan to deliver solutions for their customers or inventions for breakthrough markets.
For further information on Titan’s range of liquid flowmeters visit https://flowmeters.co.uk/. To discuss a flow measurement solution for your specific OEM application, contact Titan Enterprises on +44 (0)1935 812790 or sales@flowmeters.co.uk
Treston is not just a furniture manufacturer. We offer our customers comprehensive know-how and insights on how to make their workstations and workspaces as functional as possible.
Ergonomics is always taken into account when designing a workspace and because Treston products are modular, the workstation solutions we design are cost-effective and comply with the principles of the LEAN philosophy. Our range of products with ESD protection and our expertise in ESD matters help our customers obtain safe and functional workspaces for the most demanding working conditions.
Our long history as a furniture manufacturer, more than 500,000 workstations delivered, and 15,000 customers globally are a guarantee that we know what we are doing.
In projects, our expert sales staff go through the customer’s needs, goals, current state, and processes. Based on the conversations, we then make design proposals for the spaces and furniture. Our design engineers can make the exact type of dimensional drawings that the customer needs.
Our retailers are also experts who can provide the services that you need flexibly and comprehensively. We also support our network of retailers through expert services.
At Treston, our wide selection of products and modular and adaptable workstation solutions ensures that our customers find furniture solutions to meet their individual needs cost-efficiently.
Being a manufacturer enables us to flexibly create customised solutions
Designing an individual workstation is easy and quick with our 3D Configurator software, available at 3d.treston. com. The 3D Configurator guides you through the selection of all the necessary modules and accessories for your workstation. When you have completed the design, you can send a request for a quote electronically, or save the drawing and supply list in PDF format on your own computer with a click of a button.
We also offer an assembly service. There is a comprehensive network of installation services that we use regularly at Treston, and we can also recommend, especially for use in larger projects, to speed up the implementation of changes to manufacturing facilities.
At Treston, our expert sales staff and network of retailers, our modular products, and our opportunity as a manufacturer with its own factory to form customised solutions, guarantee that we can create an efficient and functional workspace for our customers.
Do not hesitate to contact us if you are looking for a smart and functional solution for your working environment.
www.treston.com salesuk@treston.com
At the forefront of digital marketing, Engineering Update strives to bring the latest in industrial engineering in a format that provides the best usability and ease of use for its readers.
Jodie Little jodie@jetdigitalmedia.co.uk 01843 595818
Publishing House Jet Digital Media Ltd, Suite 1 & 2 Spratling Court Offices, Spratling Street, Manston, Kent CT12 5AN
Applications open 3rd January 2023
Free to enter, the Princess Royal Training Awards celebrate employers committed to training, learning and skills development who can demonstrate exceptional impact on their business. If you want to showcase your training and join an outstanding Alumni network of 600+ organisations committed to investing in learning and development, then this could be the perfect award for you.
The Awards are open to any private, public or not-for-profit organisation operating in the UK and Ireland regardless of size or sector. Whether training to tackle skills shortages in the sector, investing in graduates to reduce staff turnover, developing programmes to create a culture of inclusivity or to address gender imbalances in leadership, the Awards are open to all.
Previous Awards recipients include global multinationals such as IBM, GSK and Labcorp, well-known brands including Barclays, Dermalogica, Greene King, JCB and Santander, and engineering industry organisations large and small, including 3P Innovation Ltd, BAE Systems, Barlows UK Ltd, Bouygues Energies and Services Solutions, Electrical Distributors Association (EDA), EDM Zone Ltd and Openreach.
The Princess Royal Training Awards offer something a bit different from other award programmes. Notably, as the Awards are a standard of excellence, employers don’t have to compete against one another. They simply need to show that they are meeting the Awards’ criteria through their training programmes.
Organisations receive royal recognition for their outstanding training programmes, with an award that sets them apart from their competitors and can be
displayed on their website, communications and products.
In addition to attendance at a high-profile ceremony where successful organisations are presented with the Award by HRH The Princess Royal, recipients also become part of the alumni network of organisations that puts training best practice at the heart of their work.
“Now we are part of a community of Princess Royal Training Awards Alumni where we can continue to share best practice and learn from other organisations as we continue to grow” - 2021 recipient.
Previous Awards recipients have reported numerous additional benefits, including increased investment in training programmes, improved recruitment and retention, and incorporation of HR and Learning and Development into organisational strategy, to name a few.
The first stage of the application process is to register your interest. You can do that here: Register now
You’ll be sent a unique link for your application form, which you can fill in and submit online. Applications are open until 31 March 2023.
You’ll have lots of support along the way, as the Princess Royal Training Awards team are on hand to offer assistance through 1-1 chats, web chat and email support, as well as through virtual support workshops and ‘tea and chat’ sessions. Applicants even get the opportunity to submit a draft application in February to get helpful feedback from Assessors.
If you have any questions, you can get in touch with the Princess Royal Training Awards team at: info@princessroyaltrainingawards.com
“Many employers are making positive contributions to our wider communities and economies by up-skilling and empowering their employees. The Princess Royal Training Awards provide a platform for such employers, giving them the accolade they deserve.”
- City & Guilds President, HRH The Princess Royal
Apply
A prestigious award that celebrates and royally recognises outstanding training in the engineering industry.
The new Classic from heat transfer specialist Fulton builds on the successes of its 70-year boiler manufacturing history to deliver a vertical steam boiler that is engineered to meet its customers’ requirements
An evolution of Fulton’s original vertical tubeless design, Classic is simple, compact and built to last, and is backed by more than 100,000 boilers installed around the world.
Available with gas, oil, or LPG/Propane burners, Classic is available with outputs from 100kW to 300kW (160 to 480 kg/h) at 10.34 Barg and efficiencies up to 84%. Full steam output is available from a cold start within 20 minutes, meaning Classic steam boilers can meet the rapid steam requirements for numerous industrial applications, including pharmaceutical, healthcare, food and beverage.
Classic uses proven technology to deliver steam economically, while maintaining the rugged, robust and reliable operation expected from a Fulton heat transfer
solution. The pressure vessel is no less than 8mm thick; and the Classic's industry-leading vertical design eliminates tubes or coils that are subject to oxygen pitting, corrosion and burn out; ensuring decades of trouble-free operation. To ensure minimal downtime and maximum production availability, ease of maintenance is also a given of the Classic’s design.
Additionally, Classic steam boilers are exempt from expensive and time-consuming SBG01 non-destructive testing requirements.
For further information on the new Classic steam boiler, visit www.fulton.co.uk, email sales@fulton.co.uk or call +44 (0)117 972 3322
A � ick so� are o er ie
Good introd c on to MRP
T picall a larger gro p
In-depth so� are alkthro gh Q&A session a�er ards
T picall a smaller gro p
Whether o are considering man fact ring so� are for the first me or looking to replace an e is ng s stem, e ha e created t o online e ents to help o gain a be er nderstanding of hat MRP can do for o r b siness, in terms of efficiencies, cost sa ings and traceabilit .
The INFO E change gi es o a taster in min tes, allo ing o to see the insight so� are and MRP in ac on. The -ho r E al a on Workshop gi es o a deeper look ith a Q&A session at the end, allo ing o to make a decision and mo e for ard. Yo ill also recei e a free cop of o r book ‘How to implement a manufacturing system’ j st for a ending.
Alterna el , register to get access to o r online Demo Mo ies, broken do n b job role, hich e plain hat insight ill do for each department in o r b siness.
Book to a end at insight.com
Free book on implemen ng MRP hen o a end.
The topic of “explosion safety” is omnipresent for plant operators and OEM´s when it comes to handling or transporting combustible dusts. Despite the widespread assumption that an increased risk of explosion only exists for gases, enormous forces can also be released by explosive dust- / air mixtures.
To help minimise the risk of explosions when handing combustible dusts, it is important to understand the requirements for an explosion and the respective dust safety characteristics, which are described below. The following picture shows the fire triangle and the explosion pentagon which must be taken into account.
The following conditions must exist for an explosion to occur within a production facility or machine:
Operators of spray dryers must combat a particular type of ignition source – namely smouldering nests that can lead to spontaneous combustion if the material undergoes excessive caking. Caking occurs due to sub-optimal drying of the material and its initially high moisture content. The caked material is then insulated against the surrounding air by a build-up of moist material. The high temperatures ensure that the caked material is continuously heated until a biological reaction takes place involving protein, carbohydrate and water – known as the Maillard reaction. The Maillard reaction generates additional heat that cannot be dissipated due to the insulating layer of caked material. This process continues to accelerate until spontaneous combustion finally occurs.
Caking of this kind can build up both on the nozzles and the inner wall of the spray dryers. If the nozzle malfunctions, droplets may fall down into the fluid bed and cause further clumping. If a smouldering nest is able to form, this can ignite the explosive atmosphere inside the dryer or the downstream machinery.
How can such conditions, which are frequently encountered in practice, be prevented?
accuracy. At the same time, the realtime fingerprint analysis eliminates the cross-sensitivity to other gases in the measurement spectrum that is common in commercial gas analysers.
To ensure a reliable measurement of the operating status, samples are sucked in from all of the dryer's relevant supply and exhaust air ducts under very high vacuum. REMBE calculates the delta CO value on the basis of the absolute values measured at the individual measuring points. This value is the mathematical difference between the CO content of the extract air and the CO content of the supply air. Thus, only events that actually occur in the respective process are detected. External factors that may disturb the process can thus be ignored.
A proprietary evaluation algorithm (RFA REMBE Flow Algorithm) enables the measured supply and exhaust air values to be compared in real time. As a result, the REMBE CO.Pilot is the first system on the market that makes it possible to adjust the individual alarm limits and gas run times for the individual measuring points in the dryer's various air throughputs without any delays. The ratios of the different supply air channels and the flexible operating hours are balanced via the software and calculated accordingly in the PLC.
Thus, if an increased carbon monoxide concentration is detected due to spontaneous combustion during the process, countermeasures can be initiated immediately.
If any one of the aforementioned prerequisites is eliminated, explosion prevention has intrinsically been practised. However, if this is not possible at all times and in all operating states, explosion hazards will still be present. In this case, it is necessary to divide any potentially explosive atmospheres into zones and systematically apply safety measures.
Drying processes in particular are used in many industries to produce material, for easier storage, more efficient transport and a longer shelf life. However, the combination of moisture extraction and high temperatures creates an increased risk of both, fires and explosions.
If fires and/or explosions occur in drying plants, which are usually very large, the situation is not only extremely dangerous for the machines and the business, but especially for the employees on site.
Everything starts with the human factor, i.e. properly trained personnel for the respective processes. Optimal process control is also required to avoid caking. But without precise and reliable information/ measurements, this is virtually impossible, even for specialists. Nowadays, humidity and one of the by-products of spontaneous combustion at early stages – carbon monoxide (CO) – are used as indicators to ensure a smooth and thus safe process. However, the fact that combined measurement systems cannot clearly distinguish between these two indicators is problematic and can result in inaccurate measurements.
The REMBE CO.Pilot makes exactly this symbiosis possible!
Via a permanent comparison of recorded data with a database of stored reference gases that serve as "fingerprints" of the selected gases, it is possible to perform a one-time check in real time and thus permanently verify the measurement
This special sampling process eliminates the need for costly and error-prone gas treatment, thus ensuring that the CO.Pilot is less susceptible to faults and requires less maintenance. Furthermore, this measurement method can make recurring calibrations unnecessary. Due to the precise measurement technology and the reproducible results, false alarms and downtimes can also be avoided. And in combination with moisture measurements, the entire drying process can be optimally controlled, significantly increasing the energy efficiency of the system.
The automation world is moving swiftly towards Industry 4.0. Forward-thinking companies in every sector are merging physical systems, distributed control systems, and virtual digital data into new kinds of cyber-physical systems. Among the technologies enabling this transition is OPC UA, providing secure real-time data communications to pull the pieces together.
OPC UA meets the needs of Industry 4.0 in ways that its predecessor, OPC DA could not. It can run on any platform, not just Windows. It has robust network support, a more sophisticated security model, and it is being developed to integrate with many other specialized industrial protocols. Small wonder that OPC UA is the protocol of choice for many Industry 4.0 projects.
However, there is still a huge installed base of preIndustry 4.0 legacy equipment and systems out there. Many of these use the OPC DA protocol for data communication. A wide range of existing OPC client applications, like HMIs and DCSs, support OPC DA. On the other hand, many legacy devices connect using OPC DA servers. This OPC DA-enabled hardware and software will be in place for years to come.
The quickest and most cost-effective way to bring a legacy OPC DA-based system up to Industry 4.0 standard is simply by using a DA/UA software gateway. This kind of middleware tool can connect an OPC DA server to an OPC UA client. Or an OPC DA client to an OPC UA server. Effectively, it provides instant OPC UA connectivity for any OPC DA server or client.
Moving to Industry 4.0 is a huge undertaking, requiring shifts in attitudes, hardware, systems, and software. But at least one problem is solved—communicating between OPC DA and UA.
Find out about Skkynet’s DataHub OPC Gateway solution.
The signing ceremony took place on November 1st, in Hanoi, Vietnam, within the framework of Vietnam-Denmark Business Summit Forum 2022, organised by the Embassy of Denmark in Vietnam, Vietnamese Government Office and the Vietnamese Ministry of Foreign Affair in Denmark.
Through this alliance their first Smart factory and transform the traditional jewelry manufacturing process with digital technologies like Robotic Process Automation, Artificial Intelligence, and more. The new manufacturing plant is set to be completed by the end of 2023 in Hoa Lac Hi-tech Park, Vietnam's first and largest hi-tech industrial zone.
The newly established partnership also transforms Julie Sandlau's operations and work processes, from human resources, operational management, to accounting and so on. FPT Software's automation and robotic processing solutions help ease the usual back-office procedures, reduce workload and workforce, thereby promoting and accompanying Julie Sandlau's towards sustainable development. The strategic step also allows Julie Sandlau's to expand its operations to a strategic market like Vietnam and target potential customers here.
FPT Corporation Chairman Dr Truong Gia Binh said. “In the past five decades, Vietnam and Denmark have established a strong relationship, with many deals among companies of both countries. With this partnership with Julie Sandlau, FPT believes that we can help reinforce the tight relationship between both nations.”
“As Vietnam’s leading IT solutions provider, FPT is confident to help Julie Sandlau with their digital transformation process and expansion goals”, Chairman Binh added.
“Vietnam always has a special place in our hearts since we started our business in 2006 here in Hanoi, so we are very excited to continue our Vietnam journey investing and developing further into digitalization, AI, blockchain technology and robotics.”, said Julie Sandlau’s CEO Soren Roed Pedersen.
“For years we have been first movers with our strong focus on ESG and we are now ready to start our digital transformation together with FPT and thus further proving the great collaboration between Vietnam and Denmark. We find the core values and vision of FPT and Julie Sandlau are a great match as we aim to transform a jewelry industry from traditional manufacturing methods to a modern digital hub. We have obviously great ambitions for our partnership with FPT as our long term strategy for Vietnam will develop into much more than just manufacturing.”, he further added.
On nurturing and developing human resources, FPT Software will transfer expertise and provide comprehensive training to Julie Sandlau's employees in Vietnam, with a deep dive into Artificial Intelligence applications. This practice will turn Julie Sandlau the world's first jewelry manufacturer to involve emerging technology in its production process, supporting its goal of becoming a digital transformation hero in premium accessories production by 2025.
The strategic partnership allows the two companies' employees to exchange knowledge and experiences, with Julie Sandlau offering fresh graduates from FPT University and FPT Corporation's staffs internship and employment opportunities. The program aims to improve educational quality and develop a guaranteed career path for future industrial engineers for FPT
https://www.fpt-software.com/
Drawing upon an extensive library of proven lens designs, nuclear industry specialistsResolve Optics can quickly design and produce a custom radiation tolerant lens to exactly match your camera / sensor and application.
Over the last 20 years, Resolve Optics has supplied many hundreds of radiation tolerant camera and sensor lenses for monitoring radioactive processes in nuclear power, reprocessing and waste storage plants.
Mark Pontin, Managing Director of Resolve Optics said “Producing clear, sharp images free of a strong yellow tint has always been a drawback when using radiation tolerant lenses on colour sensors. Tasked by a leading nuclear systems integrator to provide a solution to this problem we custom developed a 10x zoom lens able to provide High Definition (HD) images and still maintain high radiation tolerance. Whilst the yellow tint of cerium-doped glasses cannot be completely eliminated, through careful selection of specialist materials we have managed to minimise the yellow tint. This radiation tolerant 10x zoom lens provides 1080-pixel resolution and can be used on both 1/3rd and 2/3rd-inch format colour sensors. The lens can also be supplied with a
motorising package that will drive zoom, iris and focus movements. Benefiting from a tracking zoom design, once you have set this lens up on your colour sensor it will remain in sharp focus”.
Manufactured to the highest quality standards from cerium doped glass, Resolve Optics radiation tolerant lenses can withstand radiation exposure of up to 100 kGy (100,000,000 rads) and temperatures up to 55 degrees centigrade without discoloration.
To discuss development of a radiation tolerant lens optimised for your camera/sensor and application please contact Resolve Optics on +44-1494-777100 or sales@resolveoptics.com
For further information on radiation tolerant lenses please visit www.resolveoptics.com/nuclear/
Resolve Optics offers an extensive range of nonbrowning (radiation tolerant) fixed format and zoom lenses for use in environments subject to radiation. All these lenses are manufactured to the highest standards of quality and performance.
In 2019, total factor productivity in food and drink manufacturing increased by 1.8 per cent1 with UK factories striving for greater processing efficiency. Fortress Technology critically establishes itself as a crucial contaminant detection specialist and high-profile UK food manufacturers are expressing strong interest in its performance-driven Raptor metal detector and checkweighing combination machine.
Flexible, fast and affordable, The Raptor Combi is Fortress Technology’s first fully integrated checkweigher and metal detector. Winner of Food Processing’s Lean Manufacturing award in 2021, judges commended the Raptor Combi for its “innovation and useful range of food production solutions”, highlighting the natural synergy between checkweighing and metal detection.
Designed for various applications (including confectionery, bakery, meats and fish, cheeses and ready meal products), Fortress has engineered a technologically-advanced machine able to match the high-end results seen in expensive combination equipment, at a better price to performance ratio.
Notably, the Raptor Combi has the ability to accurately inspect and check the weight of large size package formats weighing up to 8kg and measuring 300mm by 400mm. Inspecting up to 150 packs per minute, the Raptor checkweigher also calculates Average Finished Weight Variance to maximise productivity.
Solving several issues that the combination inspection market previously failed to address, the Raptor Combi answers demands from UK-based food factories for more innovative fixings and connection features, such as interlocking infeed and outfeed panels, allowing processers to customise the machine to their production layout.
The Raptor Combi also introduces a unique tight-fitting conveyor and ‘no-tool’ maintenance concept. Overcoming the longstanding industry challenge of loosening belt tension during machine sanitation, operators can unclip and disconnect the conveyor motor and lift out the entire conveyor assembly for maintenance and cleaning in seconds.
As well as offering cost savings for end-users, the Fortress machine proves the power of systematic digital data capture. For UK food processors supplying multiple retailers, the Raptor Combi introduces a failsafe and fully-auditable Code of Practice (COP) test routine to further fine-tune productivity processes.
Instant HACCP and COP compliance was a key rationale for an Ireland-based bioceutical start-up Soothing Solutions installing the Raptor Combi for their new Tonstix innovation. Company founder Sinéad Crowther comments: “The Raptor Combi is very user friendly. It is the smartest piece of technology on our new production line. The screen collates all the production data we need. It ensures full weighing accuracy, extremely sensitive metal contaminant detection levels, full traceability and exceeds all of our COP compliance requirements.”
Featuring a swipe touchscreen HMI and paperless audit software with unlimited pre-programmed COPs, the robust Raptor Combi captures the data required to
1 Total Factor Productivity of the United Kingdom Food Chain 2019 – final release, gov.uk, URL: here.
guarantee food-brand integrity and absolute traceability. The machine automatically alerts the Quality Assurance manager each time a test is overdue and an in-built USB means Fortress Technology simply issues an upgrade as new COPs are introduced.
The award-winning Raptor Combi combines affordability with a digitised and futuristic approach to inspection, making the entire system is secure, hygienic and fully engineered for optimum efficiency.
www.fortresstechnology.co.uk
Fraser Technologies works with a pioneering, midlands-based aerospace engineering company to provide extremely high levels of cleaning performance for their mechanical components.
The company is world-renowned in highspeed jet engines, so the requirement for precision and superior levels of cleanliness is easy to understand. Each part needs to be spotlessly clean – with maximum particle sizes of just five microns – in order to perform its role. The team uses a coordinate measuring machine (CMM) to ensure each component is machined to very accurate tolerances. The tolerances for measurement are just five microns, so even small particulate material has an impact on this process.
With demand for ever higher levels of cleanliness and increased efficiencies across the business, the company identified that improvements could be made in some of their component cleaning processes. They had been using an aqueous system, however the failure rate on the MMI system was around 70% due to contamination, and Fraser Technologies was keen to trial a solvent solution, which they believed would deliver the best results.
Fraser Technologies recommended Opteon™ SF79®, which can remove particulate down to submicron levels without leaving residues, and has strong environmental credentials with a Global Warming Potential (GWP) of less than 15. Opteon™ SF79® was already used elsewhere in the business and had been approved on site, so they had confidence in its credentials and capabilities. Opteon™ SF79® has recently been superseded by SF80®, which has a GWP of less than 2.5.
Along with the solvent, Fraser Technologies proposed an innovative, bespoke machine, which offered increased automation
and much better linkage. This provided immediate time and cost savings and futureproofs the machine, with an option for faster washes and increased loads when required.
Since instalment in June 2019, the company has seen no failures on the CMM system due to poor cleaning, and a 100% success rate for cleanliness for these components. It has also reduced rework and lead times, and allowed for increased volumes, saving significant time and money.
The company’s manufacturing engineer in charge of the process, said: “The 100% cleanliness success rate is exactly what we were looking for. The process is significantly more efficient, reducing lead times and costs.”
To read the full case study, please click here
The fourth industrial revolution, or industry 4.0 or 4IR as it’s become known, proposes rapid acceleration of business through technology interconnectivity and next generation automation. Human intervention will be minimised – the future is digital.
Digitising every step of a business process enables companies to reimagine how their products and services are designed and engineered, sourced and supplied, manufactured and serviced (if required) once shipped. But are we really thinking that far ahead in the packaging and label industry?
But for a few exceptions, the answer has to be no. Being honest with ourselves, automation has always been the driving force of the industry – volume and speed often being the name of the game driving competitiveness. However, this has been about individual machines or process capabilities, not the joined up, hyper-connected, data-driven world that Industry 4.0 proposes.
There is no doubt that printing, converting and packing machines are getting faster, more consistent, versatile and user friendly – indeed printing or packing at a touch of a button is nearly a reality. However, the connected workflow across machines, business functions and to the external world, across customers and suppliers, is still left wanting. And yet, the industry is crying out for design and production agility to meet today’s brand and retailer needs.
With today’s ageing packaging industry workforce, the IT literate, skilled leadership required to deliver the programme can often be missing too, and the resulting culture change needed to embrace new technology and new working patterns can be daunting. The industry already has skilled labour shortages – adding new IT requirements to the mix can feel like a step too far in what is already a challenging market environment.
Instead of worrying about what we have to lose, we must focus on what we can gain in a more streamlined, efficient and satisfying work environment.
The reality is that the packaging industry is ready for change. Whether it's economic and global supply challenges, the ageing workforce, inability to attract young talent or a general recognition that ‘the times are a’changing’, the scene is set for digital disruption. What we need now are some brave leaders with a clear understanding of what can be achieved and how, and Industry 4.0 can quickly become a reality delivering the competitiveness, resilience, and versatility that today’s industry so badly needs.
Leaders from across the cutting edge of packaging will gather together on February 15 & 16 at Birmingham NEC to discuss this new frontier for the industry at Packaging Innovations & Empack, Featuring Contract Pack & Fulfilment. Attendee tickets are available to book now, for free, at www.packagingbirmingham.com
This is an abridged article that can be read in full here.
Railtex will gather the UK’s railway industry from 9 - 11 May 2023 at the NEC in Birmingham. Renewed public interest in rail travel and the need for more digitalised and greener solutions are driving the attention of many key players towards more innovative and sustainable mobility. The upcoming Railtex edition is an unmissable opportunity for railway professionals to discover the latest innovations and technologies in person, learn more about topics that move the industry from decarbonisation to digitalisation and meet business partners and new suppliers from around the world.
For more than 25 years, Railtex has been the UK's showcase event for the rail industry and it continues to reunite all stakeholders of the rail sector and its key players, including rail operators, infrastructure authorities, vehicle builders, suppliers, rail transport policymakers and planners.
Despite the challenging times the industry has been facing over the past two years, Railtex confirms to be a trusted industry event, playing a crucial role in companies’ recovery strategies in the aftermath of the pandemic. Railtex attracts high-profile visitors with decision-making power, from management, engineering, planning and technical design backgrounds looking for innovative solutions for all areas of the railway supply chain. Its visitors come from all key industry sectors, including main line passenger and rail freight operators, rail regulation and safety bodies, infrastructure contracting and maintenance, national, regional and local government transport agencies, and many more. Visitor companies at the previous edition included ALSTOM, Avanti West Coast, Bombardier Rolling Stock, East Midlands Railway, High Speed 2, Hitachi, London Underground, Mott MacDonald Ltd, Network Rail, Siemens Mobility Ltd, Transport for London, West Midland Trains, and many more.
“Looking towards 2023, these are exciting times for the rail industry. The sector will not only continue to benefit from new opportunities, such as the ongoing rail projects from North to South and East to West in the United Kingdom, but also continue to grow amongst the challenges the rail sector has been confronted with.” says Olaf Freier, Railtex Portfolio Director, on behalf of event organiser Mack-Brooks Exhibitions.
Numerous exhibitors have renewed their attendance for the upcoming edition, testifying the influence of Railtex in the UK rail market; Stadler Rail, EAO Ltd., Tidyco Ltd., Frauscher Sensor Technology, Hayley Group Ltd. and many more will be showcasing their products.
Railtex provides suppliers to the railway sector with a unique marketing platform to conduct business. It gives the industry a chance to present an impressive array of technologies and innovations, ranging from total railway systems to the smallest specialised components. “Railtex is the place to be for the whole railway industry to meet under one roof and to experience products and equipment in action, and we look forward to welcoming the rail sector in Birmingham next May.” comments Olaf Freier, Railtex Portfolio Director, on behalf of event organiser Mack-Brooks Exhibitions.
You can see the list of exhibitors on the website. Companies interested in showcasing their products and services to a specialised audience at Railtex 2023 can reserve their stand space via www.railtex.co.uk/en-gb/exhibit.html
Seminars and conferences hosted by high-level industry experts and speakers are in the programme which will be organised by the main show partner RIA, the Railway Industry Association for railway suppliers in the UK. The extensive supporting programme will provide valuable insights into future trends in railway technology and will feature a broad range of topics and sessions to address key challenges and opportunities facing the rail industry in the coming years. The show’s recurring features also include an On-Track Display and Plant & Machinery Exhibits for live machinery demonstrations, allowing companies to discover the latest technology in person and experience products and services from more than 180 different categories.
The event is organised by Mack-Brooks Exhibitions, part of RX Global, which organises targeted B2B exhibitions around the world in various industrial sectors. It is a leading organiser of the most important railway shows in Europe, including the following partner shows:
• SIFER: 28 - 30 March 2023, Lille Grand Palais, Lille, France
• EXPO Ferroviaria: 3 - 5 October 2023, Fiera Milano Rho, Milan, Italy
For more information on Railtex please visit: www.railtex.co.uk
As engineering managers come under pressure to meet demanding schedules, often with fewer skilled hands and tighter budgets, the benefits of professional tool storage and management become stronger than ever.
Snap-on Industrial’s Level 5™ automated total asset management system brings order to any workplace, enabling engineers and technicians to know exactly where to find every tool they need, when they need it, saving time and easing stress.
How useful would it be if all valuable tools could be tracked from one central point? Snap-on’s Level 5™ system makes that possible. It provides complete reports on everything
managers or supervisors need to keep an eye on.
And then there’s FOD. The threat of foreign object damage is a real and present danger in many engineering workplaces. Using Snap-on Level 5™ minimises the risk of human error, as automated tool control constantly tracks every tool and detects which tools have been removed or returned, ensuring greater protection against FOD.
Engineered to track individual tools by user, without bar codes, scanners, RFID tags or other add-ons, the system works at the speed its users demand. Other systems require additional steps to scan or log activity. The Snapon system does this automatically so users save time and don’t have to depend on other steps to ensure accurate results.
Snap-on’s Level 5™ ATC boxes are network ready, using either Ethernet or wireless connection. That enables users to review activity at all Level 5 boxes in their location from one central computer, avoiding the time consuming need to inspect each box.
Major benefits of the system include:
• No individual tool scanning required;
• No RFID tags to install or replace;
• No limitations on tool size: from ¼” screwdriver bit upwards;
• Intuitive interface, with an easy to use touchscreen
• Audible voice announcement of tool removal and replacement
• Automatic locking for maximum security
• Errors announced and displayed to indicate incorrect tool position or advise when a drawer is not closed.
Says Richard Packham, Director UK & Europe for Snap-on Industrial: “Snapon’s automated system takes asset management to an entirely new level. The ability to monitor several boxes from one central computer offers a huge advantage to engineering managers.”
For technical information visit: www.snapon-industrial.co.uk; call (01536) 413904 or e-mail: ukindustrialmarketing@snapon.com
Wolf Safety have introduced a powerful new range of ATEX certified LED installed lighting, designed for permanent use in potentially explosive atmospheres.
The world’s leading manufacturer of portable and temporary ATEX and IECEx certified hazardous area safety lighting, Wolf have been keeping people safe for more than 110 years.
The company’s designers and production engineers have now brought their vast knowledge and expertise to bear on a new range of highly effective LED installed lighting, which is safe to use in Zones 1 and 21 hazardous areas.
The range includes:
• Linear luminaires featuring the new, revolutionary Directional Linear Optics (DLO) or standard Forward Facing Array LED configurations (with battery back-up emergency versions also available);
• Floodlights with a market leading maximum light output of up to 25,932 lumens;
• Bulkhead lighting, also featuring DLO (with battery back-up emergency versions also available);
• High bay lighting.
DLO directs light exactly where it’s needed and is ideal for use in specific, close-up workspaces, reducing glare to avoid people being ‘blinded’ by the emitted light, while its excellent colour definition facilitates safety critical hazardous area tasks.
Forward Facing Array (FFA) technology can be preferable for safely illuminating large hazardous areas which need wide, even and bright light coverage, where lights are mounted away from people or at heights where glare and intensity can’t have an adverse effect on the working environment.
Says Miles Jackson, Wolf Safety’s Sales and Marketing Director:
“We know that users of Wolf products trust us to keep them safe, especially when they need to work in highly volatile atmospheres and other hazardous workplaces.
“All the values people expect from Wolf - and are seen in our portable and temporary lighting ranges - can now be found in this new installed lighting range, which we are proud to introduce.”
For detailed technical information visit: www.wolfsafety.com